DIE RELEASE
AGENTS
DIE RELEASE AGENTS
Our TurboCast brand of release agents are widely known for their incredible thermal resistance characteristics. Reacting our proprietary silicone fluid allows us to modify the silicone chain to withstand high temperatures and resist aluminum die soldering. Also, by choosing other raw materials resistant to high temperatures, allows to solve the most aggressive soldering by structural aluminum alloys.
Wetting agents are of particular importance. They allow the release agent to rapidly “wet” the die surface, spreading around core pins and flowing into tight areas the sprayers can’t reach. Our unique wettings agents are formulated to assist in creating a uniform, evenly distributed film for superior release.
Spray Applications
-
Most popular spray method with water based release agent. Typical dilution ratios are 100:1. Volume per cycle 250 - 4,000 mL
-
Spray method usually with water based release agent without dilution. Volume per cycle <30 mL
-
Spray method usually with oil based release agent without dilution. Volume per cycle <15 mL
-
Spray method similar to MQL with an oil based release agent without dilution. Volume per cycle <15 mL. Specialized electrostatic spray equipment necessary.
-
Excess release agent dripping from the cavity is captured and reused with virgin fluid. This product line has an incredible biological stable emulsion and extra additives to prevent “rot.”
Alloys
-
General purpose cast aluminum
-
These alloys create a higher demand on the release agent materials. They are more prone to solder build-up.
-
Our Mg line contains insulators to allow the molten mg to flow and fill the die cavity.
-
Oil based for 4-slide machines and water based for hot chamber machines are available.
-
Release agent with special additives to allow the lead to fill the die cavity.
Part Type
-
Release agents with anti soldering properties and metal filling additives.
-
Thick walled, high temperature raw materials provide smooth release without excessive wax buildup.
-
Large structural castings with excellent release and metal filling properties. Formulated not to affect downstream processes.
-
Release agents for hard disk drives to 5G antenna to led street housings. These release agents will not interfere with internal electronics or magnetics.
-
Release agents for superior cosmetic finishes and easily paintable.
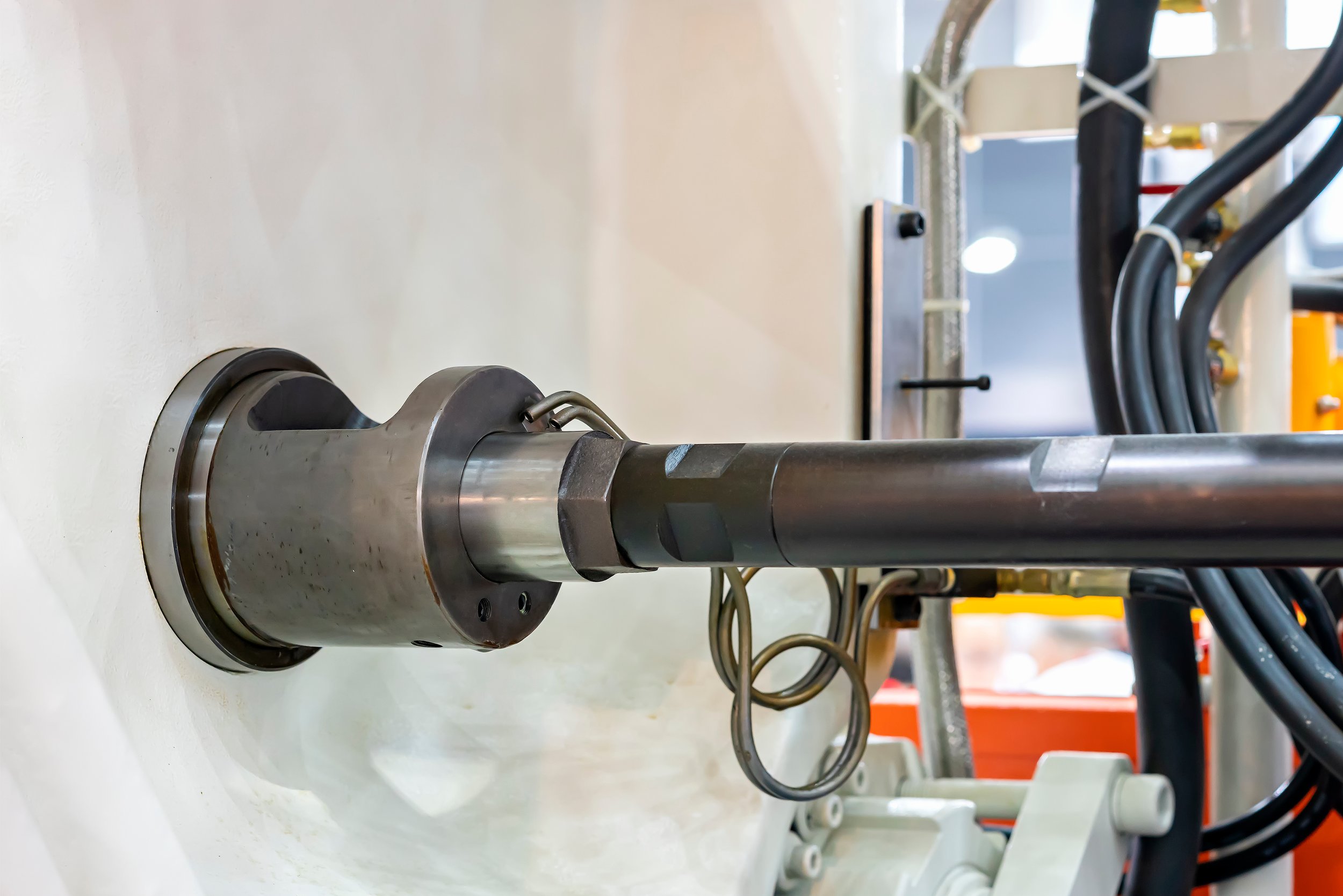
PLUNGER LUBRICANTS
PLUNGER LUBRICANTS
For decades, many casters have counted on us to drive innovation in our plunger lubricant chemistry. Our first patented product was a solid lubricant named Shotbeads®. It replaced low quality mineral oil as a lubricant and allowed our customers to gain many production efficiencies.
With the technological advancement of die casting and plunger injection systems, a new liquid plunger lubricant was born. This took matching all our previous research and rethinking the new lubricant demands. Now we will disrupt the market again, but with a liquid plunger lubricant.
TurboCast® - Synthetic Polymer based
-
Excellent metal adhesion
-
Extreme pressure additives
Boundary lubricants
Graphite and without graphite
Shotbeads® - Solid Wax based
-
Bead sizes are approximately 2mm with melt points starting at 90 °C
-
Graphite provides additional slip and lubrication
TurboCast® - Oil based
-
Depending on your application, we have a formula for small or large tonnage machines, spraying or dripping application.
-
Our oil based plunger lubricants feature excellent metal adhesion properties so the oil doesn’t drip off the plunger tip.
Ancillary Die Casting Lubricants
Water Glycol Hydraulic Fluid: Water based with high viscosity
Heat Transfer Fluid: Oil based suitable for thermal transfer units
Trim Press Fluids: Solvent, Oil, and Water based
Cold Start-up Fluids: Oil based without residue
Hot Spot Paste: Brush on with/without graphite
Slideway Lubricants: Excellent tribology properties
Machining Fluids: Synthetic & Semi Synthetic type
Cleaners: In-process & Maintenance